If you started this journey with us and read A Saddle Is Born: Part One, you know we’ve joined Pat Hooper for an inside glimpse of the custom saddle-making process. So far, the Texas saddle maker and PRCA steer wrestler has set the ground seats and is now focusing on the horn, swells, and riggings as he moves towards the back housing parts and skirt moldings around the tree.
Perhaps the most easily recognizable part of the saddle, the horn serves a variety of functions across events. For disciplines like roping, it must carry the strength of the tree to hold a dally (wrap of the rope around the horn after an animal is caught) and the ensuing weight of livestock.
When Pat approaches the horn, he wraps it, uses a pattern and press, and puts a horn cap on. He then punches holes around it and hand-sews the leather into place. The process is one of the many steps where timing matters, and the preparation required by each step must be carefully considered.
For the back housing, after cutting it out, he makes sure it fits like it is supposed to. He lines it all with latigo and ensures it won’t flare up on the back of the horse.
While his process may seem standard, he finds ways to revive lost traditions and create innovations, as is seen through his latest effort to incorporate rawhide accents back into the process and to use black wool on the underside of the saddle so it will look cleaner longer and not show so much dirt. Black wool is not easy to source, and rawhide is not easy to work with–but Pat knows what he wants and goes after it–finding a way to make it work.
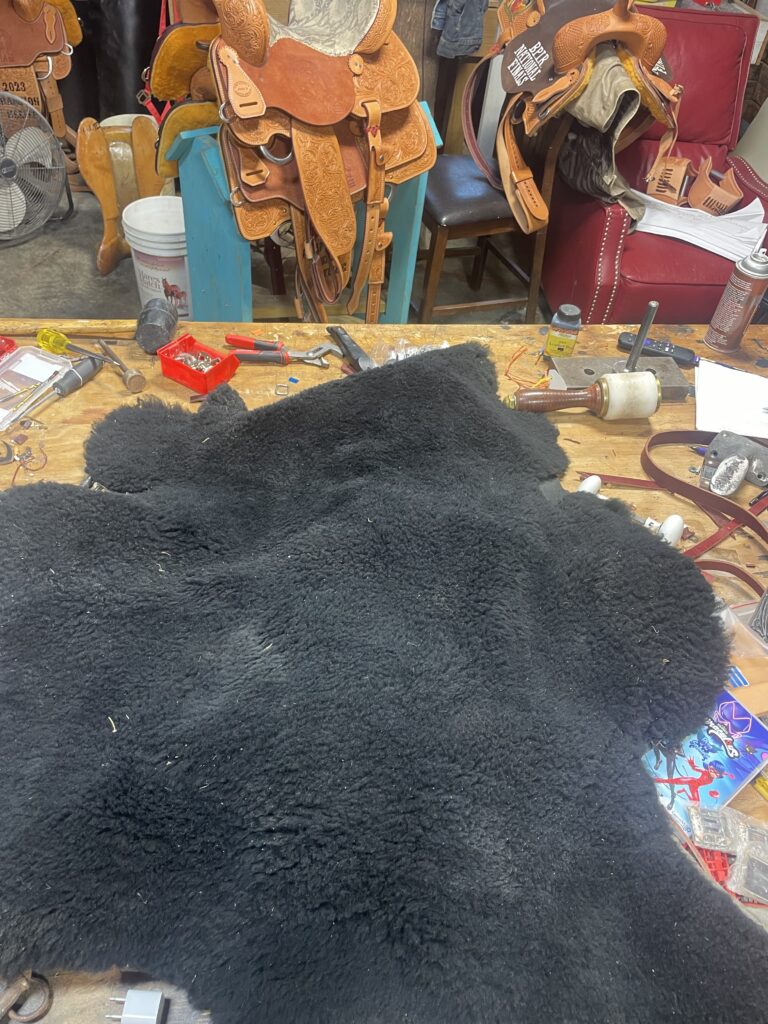
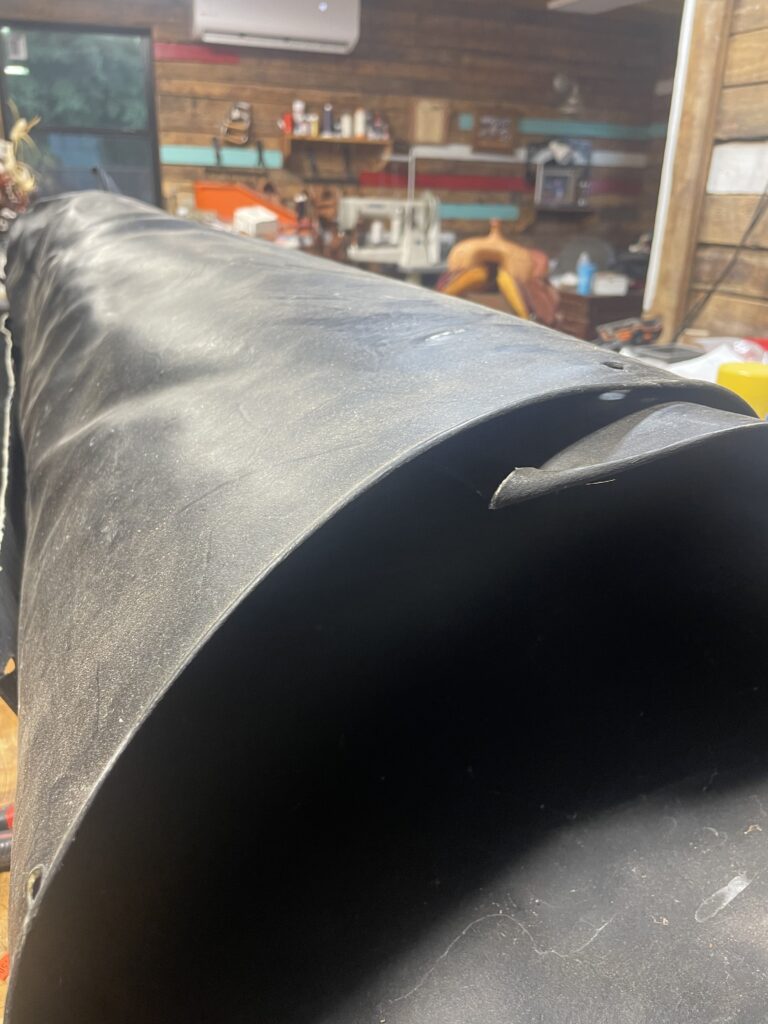
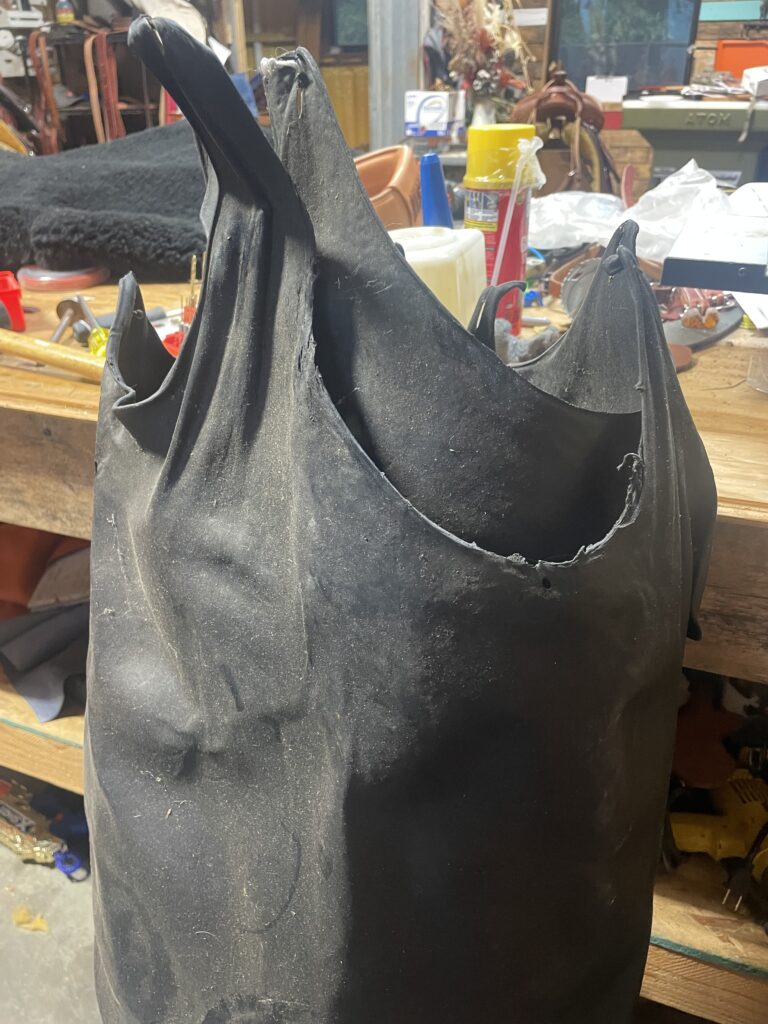
He is first in line when he locates black wool and spends extra time preparing the rawhide with a mix of water softening and freezer firming to make it pliable.
While these details keep the saddle clean and creative, he ensures functionality is front of mind. A steer wrestler himself, he’s used to steer wrestling saddles not including in skirt D rings. However, he believes by adding them into the skirt the saddle wraps around the horse better until it fits like a broken baseball glove. So, he does just that, crafting steer wrestling saddles for his bull dogging customers with in-skirt riggings. By creating a properly fitting saddle, he alleviates the need for all the different saddle pad adjustments that are often used on an ill-fitting saddle. It works–as is seen in the popularity of his saddle in arenas across the country.
As a friend and saddle making guru shared with him, if you believe in something, you should have strong conviction and a validation process. Pat does this with his own personal flair but backs up his decisions from a rider and competitor perspective. Always working to get better, he studies previous saddles he has made and learns new things at every opportunity.
When I talked to Pat, he was on his way to a rodeo, getting ready to put his saddle to use in competition. Making saddles and then putting them to the test gives him the ultimate level of understanding for what looks good, feels good and rides good.
Let’s see how these saddles take shape next! Stay tuned for part 3. In the meantime, take a look at Pat’s Facebook page: Pat Hooper Leatherwrks.
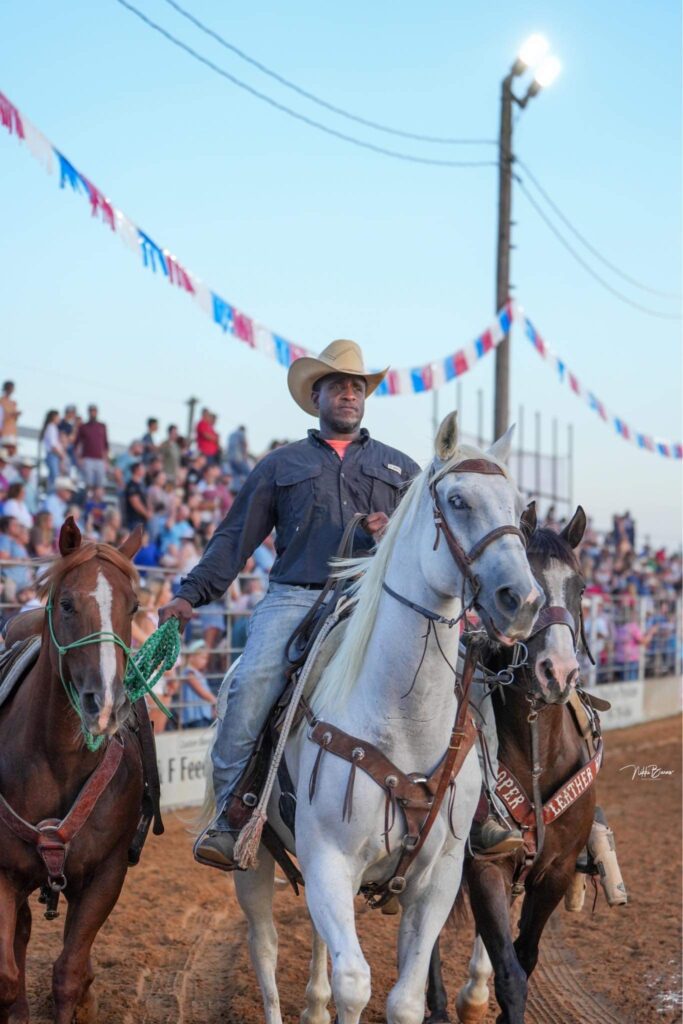
*featured image credit Lisa Moore, Moore Photography. Pat Hooper competing.